Understanding Plastic Mold Injection: A Catalyst for Business Growth
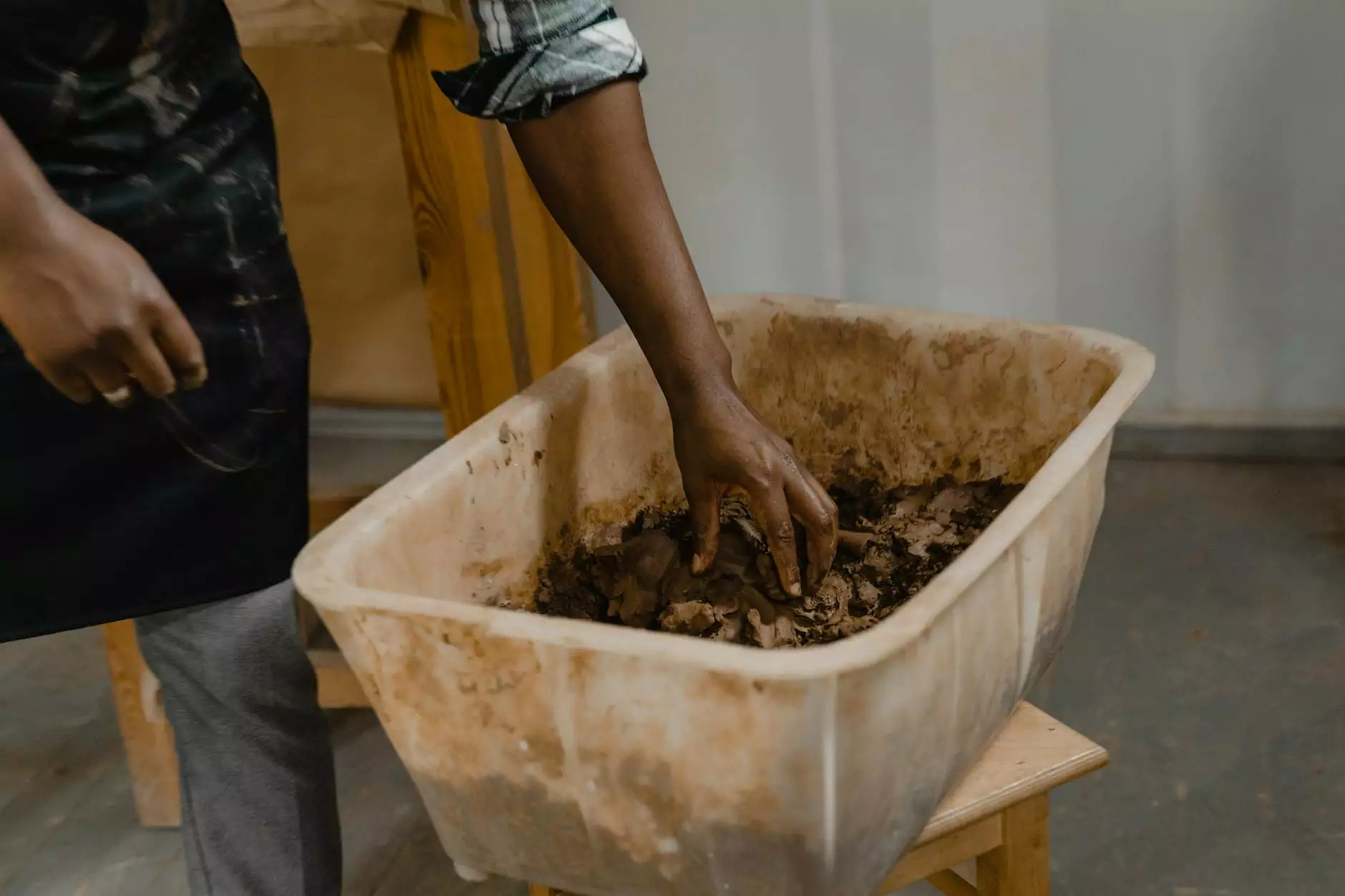
Plastic mold injection is an essential process in the manufacturing sector, particularly in the realm of metal fabrication. It serves as a pivotal means for creating various components with precision and efficiency. In this article, we will delve into the intricacies of plastic mold injection, its applications, benefits, and why it is crucial for businesses engaging in metal fabrication and beyond.
What is Plastic Mold Injection?
Plastic mold injection is a manufacturing process where molten plastic is injected into a mold to create specific shapes and sizes. This technique is widely utilized due to its ability to produce large quantities of parts with high accuracy and consistent quality. The fundamental mechanics involve:
- The use of a heated barrel, where plastic pellets are melted.
- A screw or plunger mechanism to inject the molten plastic into the mold.
- Cooling systems that solidify the plastic into the desired shape.
- A precision-designed mold that dictates the final appearance and functionality of the plastic part.
The Advantages of Plastic Mold Injection
When considering plastic mold injection for manufacturing, businesses encounter several compelling advantages:
- High Efficiency: Plastic mold injection enables mass production of components, significantly reducing time per unit and lowering labor costs.
- Cost-Effective: Once the initial mold is created, the cost per part decreases dramatically, making it an economical choice for large production runs.
- Design Flexibility: Molds can be designed to create complex shapes and geometries that would be challenging to achieve with traditional manufacturing methods.
- Material Variety: A wide range of plastics can be used, from thermoplastics to thermosetting polymers, allowing manufacturers to choose materials based on performance requirements.
- Minimal Waste: The process optimizes material usage, further enhancing its cost-effectiveness and environmentally friendly practices.
- High Consistency: The automated nature of the process ensures uniformity in production, maintaining high quality across all parts.
The Process of Plastic Mold Injection
The intricacies of the plastic mold injection process can be broken down into several key stages:
1. Mold Design
Creating a detailed mold design is paramount to the success of the injection process. Designers use CAD software to create molds that meet specific design requirements while ensuring adequate cooling and ejection mechanisms.
2. Material Selection
Choosing the right plastic material is critical. Factors such as durability, flexibility, and temperature resistance influence this decision. Common materials include:
- Polyethylene (PE)
- Polypropylene (PP)
- Polystyrene (PS)
- Polyvinyl Chloride (PVC)
- Acrylonitrile Butadiene Styrene (ABS)
3. Melting and Injection
The plastic pellets are fed into a hopper that directs them into a heated barrel. Here, they are melted and then injected into the mold under high pressure.
4. Cooling and Ejection
After the plastic fills the mold, it is allowed to cool, solidifying into the desired shape. Once cooled, the mold opens, and ejector pins push out the finished product.
5. Finishing Touches
Post-production processes such as trimming, polishing, and painting may be applied to achieve the final specifications and enhance the product’s appearance and functionality.
Applications of Plastic Mold Injection in Various Industries
The versatility of plastic mold injection makes it an invaluable asset across multiple sectors, including:
1. Automotive Industry
Automotive manufacturers rely on plastic mold injection to produce everything from dashboards and bumpers to intricate engine components. The precision and durability of the parts created via this process contribute to overall vehicle safety and performance.
2. Consumer Electronics
Devices such as smartphones, tablets, and computers utilize various plastic parts molded through injection processes, ensuring a lightweight yet durable build.
3. Medical Field
In the medical sector, precision is non-negotiable. Plastic mold injection produces components for devices such as syringes, inhalers, and diagnostic equipment, maintaining the required standards for functionality and safety.
4. Packaging Solutions
The packaging industry also benefits from plastic mold injection, where containers, bottles, and lids are all produced through this highly efficient process, allowing for cost-effective and sustainable packaging solutions.
DeepMould.net: Leading the Way in Plastic Mold Injection
As a prominent player in the field, DeepMould.net exemplifies excellence in plastic mold injection and metal fabrication. The company’s commitment to quality, innovation, and customer satisfaction sets it apart from competitors. Here’s how:
Commitment to Quality
At DeepMould.net, every project is approached with meticulous attention to detail. The company invests in state-of-the-art technology and equipment to ensure that every molded part meets strict quality standards.
Innovative Solutions
DeepMould.net prides itself on its ability to adapt and innovate. By staying ahead of industry trends and leveraging the latest materials and technologies, they provide unique solutions that meet the ever-evolving needs of clients.
Expertise and Experience
The team at DeepMould.net is comprised of experienced professionals who understand the complexities of plastic mold injection. Their expertise enables them to tackle even the most challenging projects with confidence.
Customer-Centric Approach
Understanding that each client has unique needs, DeepMould.net focuses on personalized service and support, ensuring that the final products align perfectly with client specifications.
Future Trends in Plastic Mold Injection
As we look forward, the landscape of plastic mold injection continues to evolve. Current trends shaping the future include:
1. Sustainability
With growing awareness around environmental impacts, manufacturers are increasingly adopting eco-friendly materials and practices within the plastic mold injection process.
2. Automation and Smart Manufacturing
Incorporating automation into the injection process enhances efficiency and consistency, allowing for better production management and reduced operational costs.
3. Advanced Materials
The development of innovative materials, including bioplastics and composites, expands the capabilities of plastic mold injection, presenting new opportunities across various industries.
4. Industry 4.0
The integration of IoT (Internet of Things) technologies into manufacturing processes promotes real-time data tracking, predictive maintenance, and improved production workflows.
Conclusion
In conclusion, plastic mold injection is a critical component of modern manufacturing that significantly impacts various industries. With advantages such as cost-effectiveness, design flexibility, and high efficiency, it is no wonder that businesses, including DeepMould.net, prioritize this method to remain competitive in the market. As technologies evolve and industries adapt, plastic mold injection will continue to be a driving force in product innovation and business growth.