Understanding LOLER: Significance in Business and Beyond
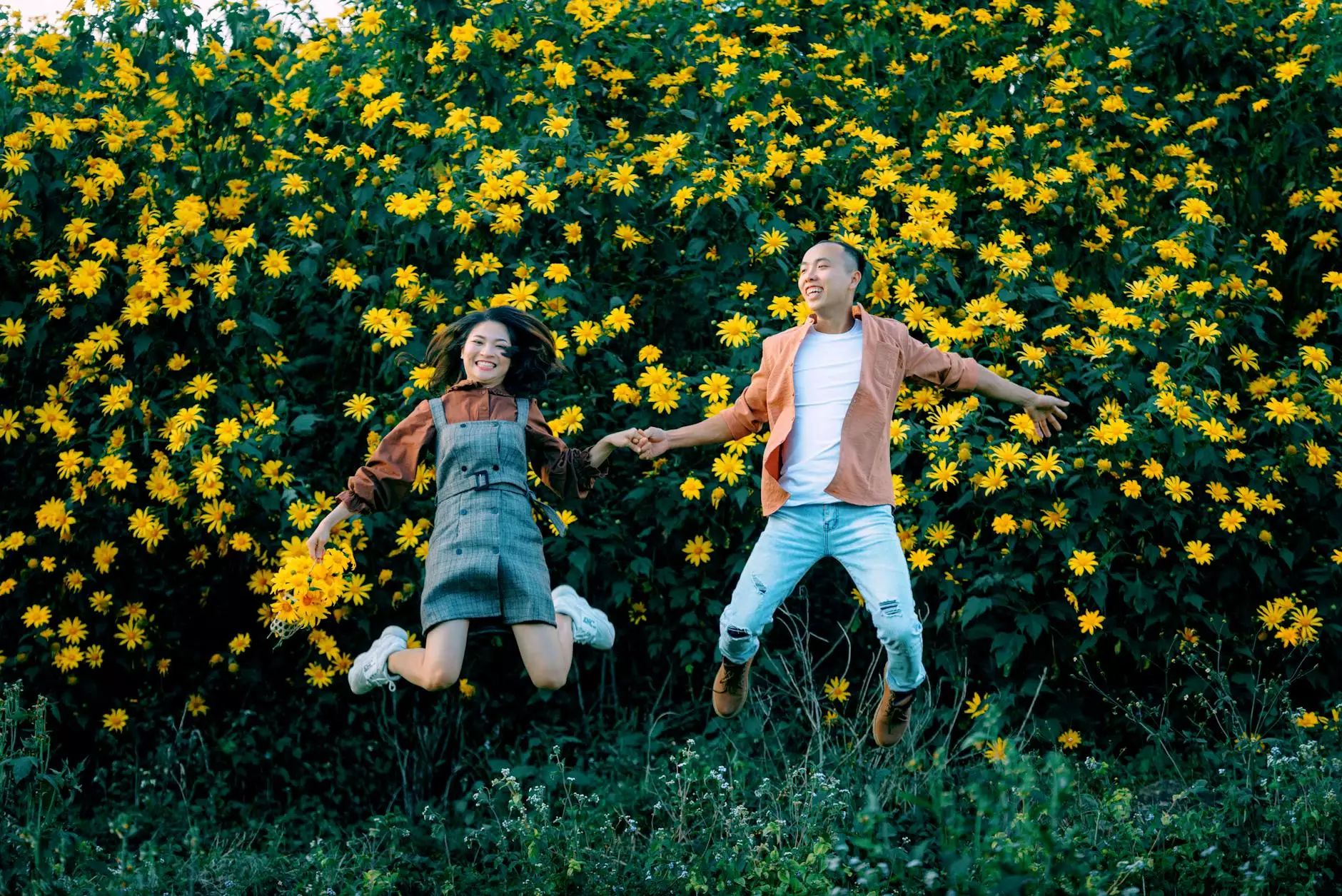
In today's competitive business landscape, understanding regulations and standards is essential. One of the key terms that often arises in the context of health and safety is LOLER. But what is LOLER meaning? The acronym stands for the Lifting Operations and Lifting Equipment Regulations 1998, which govern the use of lifting equipment in various industries. This article delves into the critical nature of LOLER, its implications in business, particularly in sectors like Home & Garden, Gardeners, and Pest Control, and how businesses can ensure compliance to enhance operational safety and efficiency.
What is LOLER?
LOLER is a set of regulations that ensure that all lifting operations using lifting equipment are safe and carried out by trained personnel. These guidelines are crucial for businesses employing machinery and equipment for lifting operations. A failure to comply with LOLER can result in serious health risks and legal consequences for businesses.
The Key Objectives of LOLER
LOLER is aimed at ensuring the following:
- Safety: To prevent accidents and injuries related to the use of lifting equipment.
- Regulatory Compliance: To ensure that businesses adhere to legal standards for health and safety.
- Training and Competence: To mandate proper training for personnel operating lifting equipment.
Importance of LOLER in Business
The implications of LOLER go beyond mere compliance; they affect overall business performance in various ways:
Enhancing Safety Culture
Implementing LOLER regulations fosters a culture of safety within the organization. Employees are more likely to operate machinery with diligence when equipped with proper knowledge and training.
Minimizing Risks and Liability
Adhering to LOLER reduces the likelihood of workplace accidents, subsequently minimizing the risk of liability for businesses. If accidents do occur, proof of compliance can significantly mitigate legal repercussions.
Improving Operational Efficiency
When lifting operations are carried out following LOLER guidelines, they become more efficient. Properly maintained equipment and trained personnel can handle tasks more quickly and effectively, resulting in time and cost savings.
LOLER Compliance Steps for Businesses
To ensure compliance with LOLER, businesses can follow these essential steps:
1. Equipment Inspection and Maintenance
Regular inspections and maintenance of lifting equipment are crucial to ensure safety. Businesses should establish a robust maintenance schedule.
2. Training and Qualification of Personnel
Ensure that all employees who operate lifting equipment are properly trained. This not only fulfills the regulatory requirement of LOLER but also enhances workplace safety.
3. Risk Assessments
Conducting detailed risk assessments before any lifting operation is essential. This process identifies potential hazards and establishes strategies for mitigating risks.
4. Documentation and Record Keeping
Maintaining detailed records of training, inspections, maintenance, and risk assessments is vital. This documentation demonstrates compliance with LOLER and can be presented during audits or inspections.
Industry-Specific Applications of LOLER
LOLER has specific consequences and applications across various sectors, particularly in Home & Garden, Gardeners, and Pest Control. Here’s how LOLER is relevant in these industries:
1. Home & Garden
In the Home & Garden industry, businesses often utilize heavy equipment for tasks such as tree removal, landscaping, and construction. LOLER guidelines ensure that lifting operations are conducted safely, protecting both workers and clients.
2. Gardeners
Gardeners frequently handle lifting equipment like lawn mowers and tillers. Complying with LOLER means ensuring that these tools are well-maintained and that users are trained to operate them safely, thus reducing potential injuries.
3. Pest Control
Pest control companies often use lifting equipment to reach high areas for inspections and treatments. Adhering to LOLER ensures that these operations are performed safely, reducing risks associated with falls and equipment failure.
Conclusion: The Business Impact of LOLER
Understanding the LOLER meaning is paramount for businesses in today's regulatory-focused environment. By prioritizing safety and compliance, businesses not only protect their employees but also enhance their reputation and operational efficiency. In sectors such as Home & Garden, Gardeners, and Pest Control, these regulations are not mere formalities but fundamental principles that drive success.
In summary, adopting LOLER principles can lead to safer working environments, lower liability risks, and improved business outcomes. Companies that understand and implement these regulations will undoubtedly stand out in their respective industries, gaining trust and loyalty from their customers.
FAQs about LOLER
What does LOLER stand for?
LOLER stands for Lifting Operations and Lifting Equipment Regulations.
Who is responsible for compliance with LOLER?
The responsibility for compliance usually falls on the employer or business owner, who must ensure that all lifting operations meet safety standards.
How often should lifting equipment be inspected under LOLER?
Lifting equipment should be thoroughly examined at least every six months, but specific requirements may vary based on the type of equipment used.
By integrating LOLER into your company's operational framework, you're not just safeguarding lives, but you’re also enhancing the overall functionality and reputation of your business.